Podstawowym kryterium oceny stabilności procesu na kartach XR, XS czy też I-MR jest obserwacja przekroczeń granic kontrolnych (ang. control limits), nazywanych również granicami interwencji lub granicami reagowania. Szerokość tych granic wyznacza się na podstawie rozrzutów w podgrupach (karty XR, XS) lub na podstawie ruchomego rozstępu (karta I-MR). Ich głównym zadaniem jest wykrywanie, czy w procesie nie wystąpiła przyczyna specjalna.
Na przykład przekroczenie górnej granicy kontrolnej (oznaczona jako GGK) na wykresie średnich oznacza, że średnia wartość pomiarów w danej podgrupie była znacząco wyższą niż dotychczas obserwowana. Taka sytuacja mogła mieć miejsce w przypadku pierwszego żółtego punktu na rysunku 1.

Jak napisano powyżej, korzystanie z wyznaczanych statystycznie granic kontrolnych ma taką zaletę, że pozwala szybko wykrywać pojawienie się przyczyn specjalnych – wartości tych granic są tak wyznaczone, aby ich ewentualne przekroczenie było dowodem (przy założeniu określonego poziomie ufności) wystąpienia przyczyny specjalnej. Ta strategia postępowania sprawdza się w przypadku procesów o umiarkowanie dobrych zdolnościach – w praktyce zwykle pomiędzy 1 a 2 (w przedstawionym przykładzie zdolność Cp=1,72).
Gdy jednak mamy do czynienia z procesem wysoko zdolnym, tak wyznaczane granice kontrolne stają się uciążliwe w stosowaniu, ponieważ nawet niewielkie wahnięcia stabilności procesu będą generować sygnały, co z kolei będzie powodowało konieczność podejmowania działań korygujących a przynajmniej wyjaśniania przyczyny sygnału. Przykład takiej sytuacji pokazuje rysunek 2. Jak widać, konieczne będzie kilkukrotne interweniowanie na skutek przekroczenia górnej granicy kontrolnej.
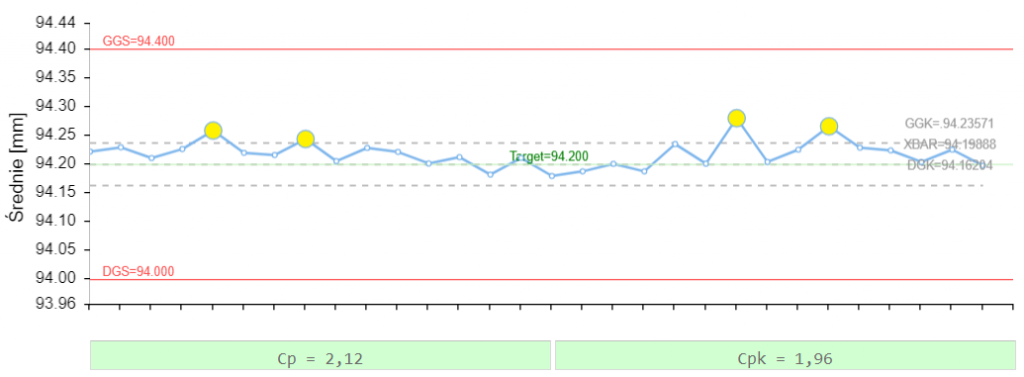
W tym momencie warto jednak zadać następujące pytanie: jakie praktyczne korzyści daje ciągłe korygowanie tak zdolnego procesu? A co za tym idzie, czy takie korekty znacząco wpłyną na jakość wyrobu, a w szczególności na spełnienie wymagań klienta? Najprawdopodobniej nie – praktyka pokazuje, że tradycyjnie prowadzone karty kontrolne XR, XS i I-MR dla wysoko zdolnych procesów stają się zbyt czułe i tym samy kłopotliwe jako narzędzie nadzoru procesu.
Spróbujmy więc odwrócić problem. Skoro mamy tak bardzo zdolny proces, może nie warto tracić czasu na jego dokładną obserwację? Może wystarczy skupić się na kontrolowaniu, czy jego zdolność jest ciągle utrzymywana na satysfakcjonującym nas poziomie, czyli powyżej wymagań klienta? Ta myśl legła u podstaw koncepcji zalecanych granic kontrolnych.
Jak wyjaśnia podręcznik SPC, tradycyjne granice kontrolne wyznaczają przedział ufności ±3*odchylenie_standardowe (σ) od środka procesu. Należy jednak podkreślić, że jest to ±3*σ (czyli 6*σ) dla wyznaczonych średnich z podgrup a nie 6*σ dla wartości jednostkowych. Jaka jest różnica między tymi sigmami, wyjaśnia wzór (1).
Uwaga: Ponieważ w dalszych rozważaniach będziemy się odnosili do estymacji współczynników zdolności w oparciu o próbę losową, zamiast symbolu σ we wzorach będziemy używali litery s, czyli odchylenia standardowego z próby losowej, która jest estymatorem odchylenia standardowego populacji (σ^).
$${s_{\bar x} = \frac{s_x}{\sqrt{n}}}\tag{1}$$
gdzie
\(s_{\bar x}\) – odchylenie standardowe ze średnich z podgrup
\(s_x\) – odchylenie standardowe z wszystkich pomiarów
\(n\) – liczba pomiarów w podgrupie
Wiemy ponadto, że zdolność potencjalną procesu wyznaczamy ze wzoru:
\[C_p = \frac{USL – LSL}{6 \cdot s_x}\]
Przekształcając powyższy wzór i podstawiając za Cp wymaganą zdolność klienta (Cpwym), możemy obliczyć, jakie powinno być 6*sx takiego procesu:
\[6 \cdot s_x = \frac{USL – LSL}{C_{p_{wym}}}\tag{2}\]
Pamiętamy jednak, że na wykresie średnich granice kontrolne pokazują 6*sigma średnich a nie 6*sigma pomiarów. Korzystając więc z wzorów (1) oraz (2) ostatecznie uzyskamy wartość 6*sigma dla średnich:
\[6 \cdot s_{\bar x} = \frac{USL – LSL}{C_{p_{wym}} \cdot \sqrt{n}}\]
Dzięki temu w prosty sposób możemy wyliczyć wartość górnej i dolnej zalecanej granicy kontrolnej:<gdzie/p>
\[ UCL_{zal} = x_{tar} + 3 \cdot s_{\bar x} \] \[ UCL_{zal} = x_{tar} + 3 \cdot s_{\bar x} \] \[ \text{gdzie: } x_{tar} = \frac{USL-LSL}{2} \]
Czyli wartość docelowa dla położenia procesu, czyli środek przedziału specyfikacji.
Po usunięciu z karty XR statystycznych granic kontrolnych i wprowadzeniu wyliczonych w powyższy sposób granic zalecanych, pokazany poprzednio na rysunku 2 wykres będzie wyglądał następująco:
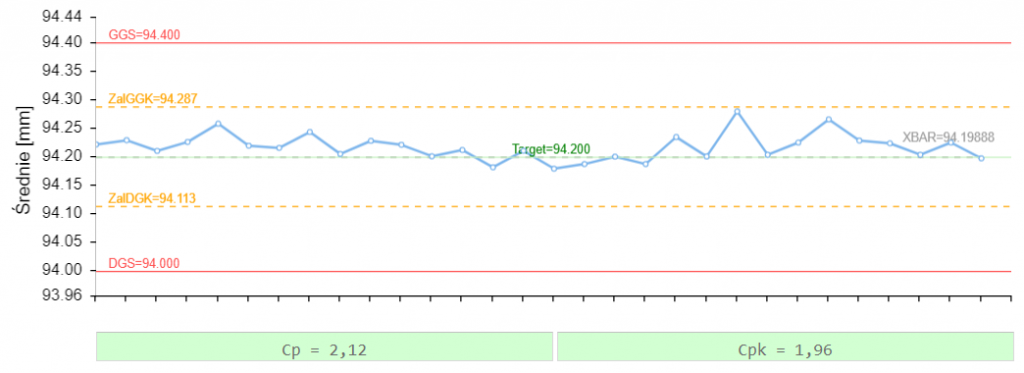
Jak widać na rysunku 3, zalecane granice kontrolne są nieco szersze od granicy wyliczonych, dzięki czemu zniknęły sygnały o przekroczeniu górnej granicy. Z drugiej strony, możemy jednocześnie bezpiecznie zakładać, że dopóki nie pojawią się punkty poza tak wyliczonymi granicami kontrolnymi, zdolność procesu wciąż jest powyżej wymagań klienta.
Opisany tu mechanizm obliczeniowy zaimplementowano w oprogramowaniu proControl, które pozwala wyznaczyć zalecane granice kontrolne w oparciu o powyższe założenia. Zachęcamy do testowania programu. Szczegóły oferty na stronie: http://procontrol.new19.pronost.pl .